Standard Operations :: Frozen Beverage :: Viscosity Controls
Spaceman USA Frozen Beverage machines are operated based on mechanical controls. The viscosity, or thickness, of the product is not based on temperature, but rather a set of controls that determines when the product has achieved a desired thickness. Below is a description of these controls, how they work, and how to verify that they are functioning correctly.
Mechanical Levers
There are two levers on the front of your machine, one that moves horizontally (Torque Lever), and one that moves vertically (Draw Lever).
- The Torque Lever is the mechanical lever that determines the product viscosity when in Freeze mode.
- The torque lever should move freely to the left and right and you should not feel any binding, sticking, or roughness. This lever activates a microswitch behind the front panel. The microswitch should be normally open when the lever is to the left, and closed when the lever is to the right which would indicate that product is at the desired viscosity, or thickness. You should be able to hear this switch clicking on and off when you move the torque lever left and right. This switch should click closed when the lever is just to the right of the center of the dispensing door.
- The Draw Lever is the mechanical lever that tells the machine when product is being dispensed from the freezing cylinder when in Freeze mode.
- The draw lever should move freely up and down and you should not feel any binding, sticking, or roughness. This lever also activates a microswitch behind the front panel. This microswitch is also normally open, and is closed when the draw handle is opened and the user is dispensing product. You should be able to hear this switch clicking closed and open when the lever is lifted about 1/4 to 1/2 of the way up.
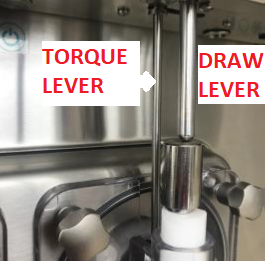

Having issues with your machine? Start with the basics. Check out the Frozen Beverage Best Practices article and ensure you have properly cleaned your machine and followed all Best Practices before assuming something is wrong with your machine. Often times a simple operational fix, like proper cleaning and lubrication, replacing the tune up kit, or not running the machine out of mix will resolve the issue.
Before performing these steps, we highly recommend fully cleaning the machine, replacing the Tune Up Kit and Scraper Blades before checking the rest of the system.
We also highly recommend ensuring your product is at an adequate Brix Level to eliminate your product being the cause of the issues.
Viscosity Controls Functionality Check (End-User)

Have a 2-Flavor machine? Perform these steps one side at a time, leave the other side OFF while performing the steps.
- Verify that the machine is plugged into the correct voltage, and the is on a dedicated circuit with no other appliances or items plugged into the same breaker. If you are unsure if your machine has the correct voltage, please contact a certified electrician.
(Solution: The machine will not work correctly if it is not on a dedicated circuit, or is not receiving correct voltage. The machine specification sheet will specify the correct voltage and circuit breaker requirements.) - Watch and carefully follow the Spaceman Videos - Frozen Beverage - Cleaning Overview video, and fully drain, rinse, disassemble, clean, lubricate and re-assemble your frozen beverage machine. Follow all steps until it specifies to add sanitizer to the machine.
(Solution: Lubricating the machine properly is very important. Use only Spaceman Food Grade Lubrication and ensure sufficient lubrication especially on the drive shaft gasket and torque rotor o-rings. If not lubricated correctly, the machine will not work correctly). - Follow the manual instructions to put a proper Sanitizer into the machine, and fill the cylinder up to the prime plug with sanitizing solution.
- Put the machine into WASH mode to sanitize
- The motor should turn on, no odd noises should be heard.
- The motor should be agitating in a clock-wise direction.
(Solution: If the motor does not turn on in WASH mode, first check your power input and breaker to ensure nothing is tripped at the building. Then, locate the thermal overload reset button on the side or rear of the machine and press it firmly to reset the thermal overload relay. It is a green button about 1" in diameter behind the panel. On some machines, the button is behind a black rubber/plastic cover. If this does not work, continue below to diagnose the issue).
- Manually move the torque arm to the right, and then release.
- The torque arm should move freely, you should hear a switch click a little to the right of center, and when released the torque arm should snap back to the left. You should hear the switch click again as it disengages with the torque arm to the left.
(Solution: If the torque arm does not move freely, investigate why. It may be sticky, not lubricated properly, or damaged. If you do not hear the switch clicking on and off, this will not allow the machine to operate correctly.)
- Place a bucket under the dispensing spout and dispense a little sanitizer, opening the handle fully, and then release.
- When the handle is opened, you should hear a switch click about half way open, and when released, the handle should close and you should hear the switch click again as it disengages.
(Note: On older frozen beverage models, the handle will not auto-return to closed and must be manually closed)
(Solution: If you do not hear the switch clicking, or the handle does not move freely, investigate why. It may be sticky, not lubricated properly, or there may be damage causing the switch not to engage. This will cause issues).
- Dispense and discard the remaining sanitizer, and return to the cleaning overview video to properly add product to the machine. It is important to fill the cylinder completely using the prime plug.
- Put the machine into FREEZE mode.
- Verify that Standby mode is turned OFF and the Standby light is not illuminated.
- The motor should turn on, and a few seconds later the compressor and exhaust fan should turn on.
- With liquid product, the torque arm should be all the way to the left.
- After 3-7 minutes, depending on the initial temperature of the product and your model, you should start to see ice particles forming in the cylinder, indicating that it is cooling.
(Solution: If the compressor and exhaust fan do not turn on, or the product does not cool down, investigate why. First, make sure the torque switch is to the left all the way. Second, make sure you have performed a preventative maintenance recently and that your condensing coil is clean and operational. If your machine is still not cooling, you may need a technician to further diagnose.)
- While the machine is freezing down, you should see the torque lever start to move toward the right. Pay close attention to this, and watch until you can hear the torque switch click just right of center.
- A few seconds after the torque switch clicks, the cooling to the cylinder will stop, and after 10 seconds or so, the motor will shut off.
(Note: On 6650, and 6455 machines, the compressor may not shut off if the hopper requires cooling. The cooling to the cylinder will shut off and a solenoid will direct cooling to the hopper which may be hard to detect with product in the hopper)
(Solution: If the motor never turns off after the torque arm is to the right and engaging the torque switch, then there is likely an issue with the torque switch or wiring that requires a technician to repair. This will lead to a freeze up. If the torque arm does not move to the right, even with the product becoming over-frozen, then either the viscosity is too high, there is improper lubrication or something binding the torque arm, or the product brix level is too low.)
- Dispense 8-10oz of product using the handle.
- The motor should turn on when the handle is raised. Cooling will only come on if the torque arm is to the left of center and the torque switch is not engaged. If the torque arm stays to the right, the motor will shut back off.
- Continue dispensing servings until the torque arm moves back to the left and disengages the torque switch. Once the torque arm is to the left while the motor is running, the cooling system will turn back on and repeat step 9 to verify the machine functionality.
(Solution: If the motor does not turn back on, inspect the draw switch and ensure that it is engaging.)
- Using a straw or other clean utensil, locate and press down on the low mix float in the hopper. This should illuminate the Low Mix Indicator. Releasing the float will turn the indicator back off.
(Solution: If the low mix indicator does not turn on or off, a technician may be required to replace the sensor if broken, or the indicator LED if burnt out. Using the small green square alarm button will allow you to determine if the sensor is working as you'll hear an audible alarm when the green square button is engaged). - For two flavor machines, repeat steps 4 through 11 on the second side.
- For machines with hopper cooling: Allow the machine to operate for several hours. During this time, the machine should detect and cool the hoppers. Use a thermometer to measure the temperature of the hopper(s), they should maintain at ~42F (5C).
(Solution: If the temperature is too warm, or too cold, first make sure that the hopper levels are kept equal if there are two hoppers, second ensure that pre-chilled product is placed into the machine. If these things are the case, then the thermostats may need to be adjusted accordingly. These are located inside each side panel and can be adjusted up or down as needed). - At the close of business, press the standby button. The standby indicator should turn on.
- When you return in the morning, the product in the machine hopper and cylinder should be liquid and at ~42F (5C) if measured with a thermometer
(Solution: If the indicator does not illuminate, the button or indicator has likely failed and needs replacing. If the temperature in the hopper or cylinder is too warm or too cold, the thermostats may need to be adjusted or calibrated accordingly. These are located inside each side panel and can be adjusted up or down as needed).