Troubleshooting :: Soft Serve :: Troubleshooting a Compressor
Introduction
This article covers the steps to diagnose and troubleshoot compressor issues with the machine. These steps are required to be performed in order to have a compressor replaced under warranty. The information collected during these steps must be provided to Spaceman Technical Service prior to receiving a warranty replacement.
Required Tools
- Metric Hex Driver or Allen key set
- Flathead Screwdriver set
- Clamp-style Amp Meter
Troubleshooting Compressor Issues
Power Troubleshooting
The first step is to check and verify the compressor is receiving the correct power.
- Follow the instructions in the Operator Manual to properly drain, disassemble, and clean the machine.
Warning: The machine must be unplugged as power may be available to certain components even with the machine power switch in the off position.
-
Turn Power Switch to Off and unplug the machine from the wall.
Using a flathead screwdriver, unlock all panel locks remove the
correct side
panels
or front panel
from the machine.
Refer to the parts list for compressor placement.
All panel locks are quarter-turn and should turn inward to unlock, they do NOT require significant force to unlock. For floor-standing machines, generally only the top panels need to be removed.
Note: For smaller countertop machines, panels may be installed using an 8mm Hex-head bolt rather than quarter-turn panel locks.
- Locate the electrical box that has a round green reset button, and remove the electrical box cover using a Philips head or appropriate size wrench
- Using a voltmeter, measure the power at the building receptacle and verify that the supplied power is within range for the machine. Please see the Electrical Guide for more information on voltage requirements.
-
Plug the machine back into the wall power
Warning: Plugging the machine in with panels off is dangerous. Be very careful to not touch any exposed contact leads, wires, etc. Be mindful of tools and what they touch as there is live voltage to components once plugged in
- Use the wiring diagram and locate the contactor that operates the compressor.
- Measure the voltage on the input side of the contactor and verify it matches the building power.
- Depress the manual button to turn on power to the compressor, and use a voltmeter to measure the output power going through the contactor. It should match the building power.
Potential Solution: If the input power to the compressor has been verified, but the compressor does not turn on when the contactor is depressed, there is an issue with either the start components or the compressor itself. Further troubleshooting steps are in the next section below. If the compressor turns on when the contactor is manually depressed, then proceed with Step 10 below
- If the compressor turns on when the contactor is manually depressed, the next step is to have the machine attempt to operate the compressor to verify the contactor is getting adequate coil voltage.
- On the front of the machine, verify the machine is completely drained of product and the dispensing door and beater assembly has been removed.
- Place the machine in Freeze mode to turn on the main compressor.
- Measure the voltage applied to the contactor coil for the compressor
Potential Solution: If the voltage at the contactor coil is 110V or 220V (depending on machine), then the contactor is bad and needs to be replaced. If the voltage at the coil is 0V, proceed with Step 14 below
- If the voltage at the coil is 0V, check the Power Board and verify that the Main Compressor relay has both red LEDs illuminated, indicating that the relay is receiving a command to turn on, and sending that command onward.
Potential Solution: If the relay has no lights illuminated for the compressor relay, check the connection of the ribbon cable between the control board and power board. If the relay has one light illuminated, the power board is bad and needs to be replaced. If the relay board has both lights illuminated, check the connection of the ribbon cable and all wires between the power board and the contactor.
- Press RESET to stop the machine function
Lock Rotor and Start Component Check
The second step is to check for a lock rotor and check if the start components are functioning correctly. The start components are easy to replace and are the most common parts to wear out first. Start component failure is most often caused by failure of the capacitor or relay due to excessive high pressure on the compressor, or a voltage drop below the machine operating voltage range. These steps assume that input voltage to the compressor has been verified per the Electrical Guide for the machine.
Warning: Risk of severe electrical shock. Anytime the machine is plugged into power, any exposed lead may contain high voltage. Be very careful to not accidentally touch or short any leads together. Use assistance as required and be mindful of tools.
- To check for a lock rotor, place a clamp-style amp-meter around one of the power wires going to the compressor.
- On the front of the machine, verify the machine is completely drained of product and the dispensing door and beater assembly has been removed.
- Depress the manual button on the contactor to turn on power to the compressor, closely monitoring the compressor amp draw.
Potential Solution: If the amp draw measured reaches the Lock-Rotor Amps (LRA) on the compressor specification sheet, then the compressor is in lock rotor and needs to be replaced. If you do not get any or very low amp draw, proceed with steps below.
Note: When replacing a compressor, the filter dryer and start components must also be replaced at the same time. Spaceman only sells compressors as an assembly with a corresponding filter dryer and start component included for this reason. Brazing must be done in a timely manner to avoid excess moisture and debris entering the system. Use water-soaked towels as necessary to wrap and protect sensitive parts such as solenoids.
- Power off and unplug the machine from the wall
- Depress the manual button on the contactor as if you were trying to manually turn on the compressor to discharge the start capacitor.
- Open the start components for the compressor. These are sometimes located in a plastic enclosure and sometimes on the side of the compressor.
- Using a voltmeter, measure the capacitance of the compressor start capacitor and verify that it is within range for the capacitor being measured. This specification should be labeled on the capacitor.
- To check the start component relay, measure for continuity through the relay with and without the manual contactor depressed. Specific details are below.
Potential Solution: If either the capacitor or relay in the start components is bad, the start components need to be replaced.
Note: When replacing the start component, we do not recommend loosening or removing the connector from the compressor, as it risks the connections becoming loose and causing other failure. Instead, replace the start components using the wiring already inside the machine.
Checking Relay on Tecumseh Compressors
Warning: Risk of severe electrical shock. Anytime the machine is plugged into power, any exposed lead may contain high voltage. Be very careful to not accidentally touch or short any leads together. Use assistance as required and be mindful of tools.
These steps will be similar on all compressors, this example explains the process for the main Tecumseh compressors used in Spaceman machines
.
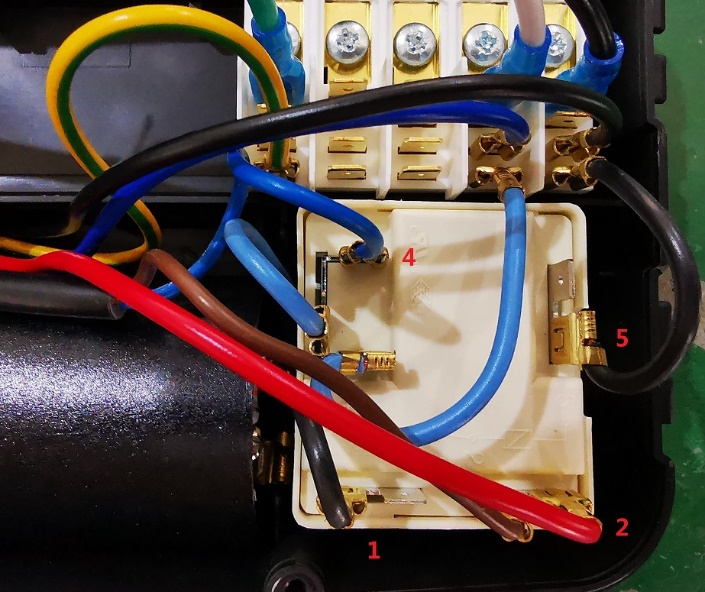
- Power the machine off.
- Use a voltmeter to measure continuity between terminal 2 and 5. You should measure low resistance showing continuity.
- Use a voltmeter to measure continuity between terminal 1 and 2. You should measure low resistance showing continuity.
- Use a voltmeter to measure the voltage at terminal 2. Manually depress the contactor to turn on the compressor while monitoring the voltage. You should see adequate voltage for the compressor at terminal 2 with power is applied.
- Repeat step 4 above to measure the voltage at terminal 4. You should see adequate voltage for the compressor at terminal 4 with power applied.
- Repeat step 4 above to measure the voltage between terminal 2 and terminal 4. You should see adequate 220V voltage between these two terminals.
-
Use a voltmeter to measure the continuity between terminal 1 and 2, this should show continuity with power off. Manually depress the contactor to turn on the compressor while monitoring voltage. You should see an open circuit, or no continuity between terminal 1 and 2 with power applied.
Potential Solution: If terminal 1 and 2 remain shorted, or power is not applied to terminals 2 and 4 when the compressor is powered on, the start components need to be replaced as the relay has failed. If voltage is properly applied, and the continuity checks correctly, the start components are likely good and the issue is with the connection to the compressor, or the compressor itself.
Note: When replacing the start component, we do not recommend loosening or removing the connector from the compressor, as it risks the connections becoming loose and causing other failure. Instead, replace the start components using the wiring already inside the machine.
Checking the Compressor for Winding Failure
The final step is to check the compressor itself for failure. Compressor failure is the least common issue, however winding damage can occur if the compressor is constantly run at too high of pressures or without refrigerant. It is also possible that the electrical connection to the compressor is not good and needs to be repaired or replaced.
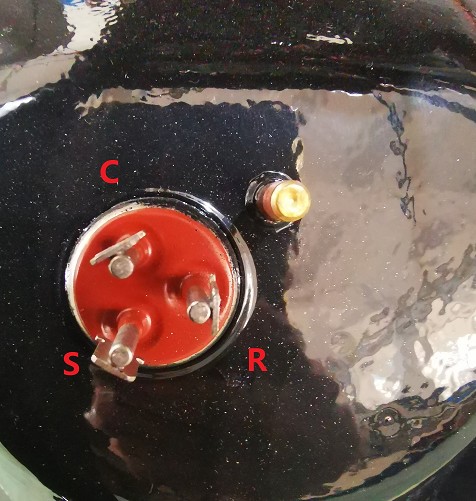
- Power off the machine and unplug from the wall.
- Depress the manual button on the contactor as if you were trying to manually turn on the compressor to discharge the start capacitor.
- Check the connection of the wires connected to the compressor. You can check these wires by removing the cap and inspecting the connection of the spade connectors to ensure everything is tight and secure.
- Plug the machine into wall power.
- Use a voltmeter to monitor the voltage input to the compressor.
- On the front of the machine, verify the machine is completely drained of product and the dispensing door and beater assembly has been removed.
- Place the machine in Freeze mode to turn on power to the compressor
- Adequate voltage should be applied to the compressor at the spade terminals. (Ex. For most 220V compressors, 280-310V will be measured input to the compressor).
Potential Solution: If you measured good voltage at the start component relay, but not at the compressor, there is likely an issue with the wiring or connectors between the start components and the compressor.
- Power off the machine and unplug from the wall.
- Depress the manual button on the contactor as if you were trying to manually turn on the compressor to discharge the start capacitor.
- As a last resort, check the continuity on the windings of the compressor to determine if the compressor windings have failed. For all compressors, there are three terminals: S (Start Winding), R (Run Winding), and C (Common). Use a voltmeter to measure and notate the resistance between all of the windings (S-to-C, R-to-C, and R-to-S). If the compressor windings are not marked, please refer to the compressor specification sheet for correct winding diagram.
-
The resistance should match the following equation: SR = SC + RC. For example, if S-to-C = 5.6 ohm, and R-to-C = 1.3 ohm, then S-to-R should measure 6.9 +/- 0.1 ohms.
Potential Solution: If there is no resistance between windings, OR the equation is not satisfied and has too much error, then there is winding damage in the compressor and the compressor needs to be replaced.
Note: When replacing a compressor, the filter dryer and start components must also be replaced at the same time. Spaceman only sells compressors as an assembly with a corresponding filter dryer and start component included for this reason. Brazing must be done in a timely manner to avoid excess moisture and debris entering the system. Use water-soaked towels as necessary to wrap and protect sensitive parts such as solenoids.