Introduction
The below troubleshooting steps are to verify the functionality of the 3 Phase Motors installed on Spaceman Soft Serve machines. These steps assume that you have already verified the controls of your Soft Serve machine and have verified that the input power to the machine is adequate for the machine.
Every 3 phase motor has six (6) terminals with the supply voltage connected to three (3) of those terminals. The most common configuration of a three-phase motor is the Delta - Star (Wye) configuration with the Delta side connected to the supply voltage. The terminal configuration of a 3 phase motor is shown below.
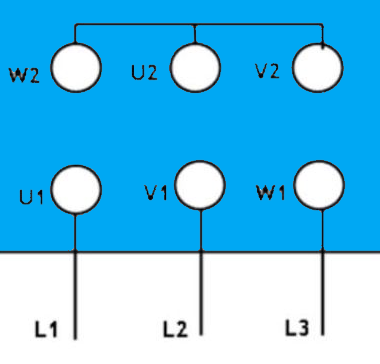
*The W2U2V2 terminal set is the star side of the 3 phase motor while the U1V1W1 is the Delta side of the motor connected to the supply voltage.
Warning: Operating the machine with the side panels off is dangerous. Please do not stick hands inside machine components while power is on.
Motor Power Troubleshooting Steps
- Remove the side panels of the machine to gain access to the drive motor.
- Remove the main drive belt(s). Please refer to the Soft Serve Replacing Belts Article for proper instructions on removing these belts
- Place the machine in Wash mode
-
Using a Digital Multimeter, measure and notate the voltage across the phases as follows: (L1 to L2, L1 to L3, L2 to L3). These measurements can be taken at the output of the Power Inverter for each motor.
Potential Solution: You should read 208-240V measured across each of these phases. If voltage is above or below this range, or there is no voltage present, check the Power Inverter driving the motor for input power and trace backward toward the power board.
-
Using a Digital Multimeter, measure and notate the voltage from each phase to ground: (L1 to
Neutral
, L2 to
Neutral
, L3 to
Neutral
).
These measurements can be taken at the output of the Power Inverter for each motor.
Potential Solution: You should read the proper voltage measured from each phase to ground. Usually, each phase will be 110-120V, with one phase being a higher voltage. If voltage is above or below this range, or there is no voltage present, check the Power Inverter driving the motor for input power and trace backward toward the power board.
- Press Reset to stop the machine.
- Locate the Power Board on the machine. You may need to remove the electrical box cover to access the power board.
- Using a Clamp-style Amp Meter, install the amp meter around the black wire running through the amp sensor on the power board and notate.
-
Press the Wash button to return the machine to wash mode
Potential Solution: If the motor does not turn on, but there was adequate voltage, check for any loose wiring between the Power Inverter and the Motor. If wiring is good, proceed to the Winding Resistance Troubleshooting steps below to check if the motor is bad.
-
On the control board, press the P button until the motor amperage is displayed. The amp draw should match the amp meter within ~0.2A. Note that there is a delay in the control board amp draw reading compared to the amp meter. With no load (no belts connected), the amp draw of the motor should be 1.1 to 1.4A for 220V machines.
Potential Solution: If the amp draw of the motor is too high, verify there is nothing binding up the motor or drive train, and proceed to the Winding Resistance steps below to check the motor functionality
- If the voltage and amp draw of the motor check out, then the motor and control system are operating correctly. Please contact Spaceman Technical Support for further troubleshooting. Please be prepared to provide all information (voltages, amp draws, etc.) to the technician to assist in providing the best next steps.
Winding Resistance Troubleshooting Steps
- Remove the side panels of the machine to gain access to the drive motor.
- Remove the main drive belt(s). Please refer to the Soft Serve Replacing Belts Article for proper instructions on removing these belts.
- Using an ohmmeter measure the resistance across the windings of the motor as shown below. The indicated terminal matrix (blue lines) shows the way the windings of a 3 phase motor should be tested with an Ohmmeter:
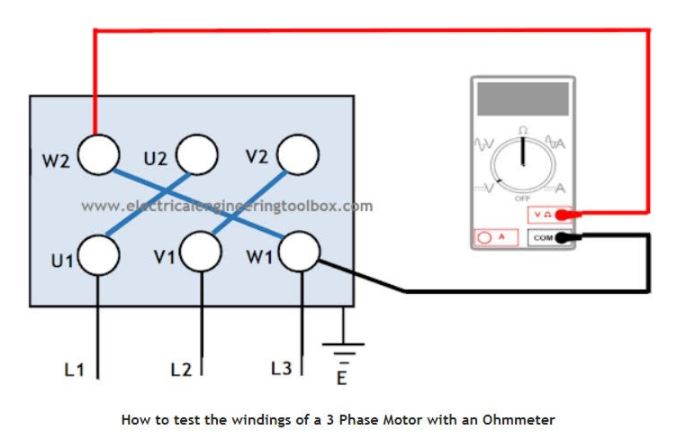
Potential Solution: If any of the terminal combinations W1W2, U1U2, V1V2 should indicate an open circuit (no resistance) then the motor is bad and needs to be replaced. The resistance measured on these pairs should all be very similar (+/- 10%). If the resistances are dissimilar, the motor is bad and needs to be replaced.
-
Using an ohmmeter measure the resistance from each power terminal to all other terminals except the pair defined above (i.e.
for U1, measure:
U1 to W2, U1 to V2, U1 to V1, U1 to W1, etc.)
Potential Solution: If any of the terminal combinations in Step 4 show anything other than infinite resistance instead of open, then the motor is bad and needs to be replaced.
-
Using an ohmmeter, measure the resistance from each of the
six (6) terminals and motor frame (E)
.
Potential Solution: If any of the terminals indicated continuity to ground, the motor is bad and needs to be replaced.
- If the motor passes a winding resistance check, then there is likely no issue with the motor and other steps should be performed to determine why the motor is not performing. Please contact Spaceman Technical Support for further troubleshooting steps. Please be prepared to provide all information (resistances, voltages, amp draws, etc.) measured to the technician to better assist in providing next steps.